Using Process Refractometers to Accurately Control Urea Dilution.
In the realm of chemical engineering and industrial processes, the dilution of urea plays a crucial role, particularly in the automotive and nitrogen fertilisation sectors. This blog delves into the intricate details of the urea dilution process, its applications, and the technology involved.
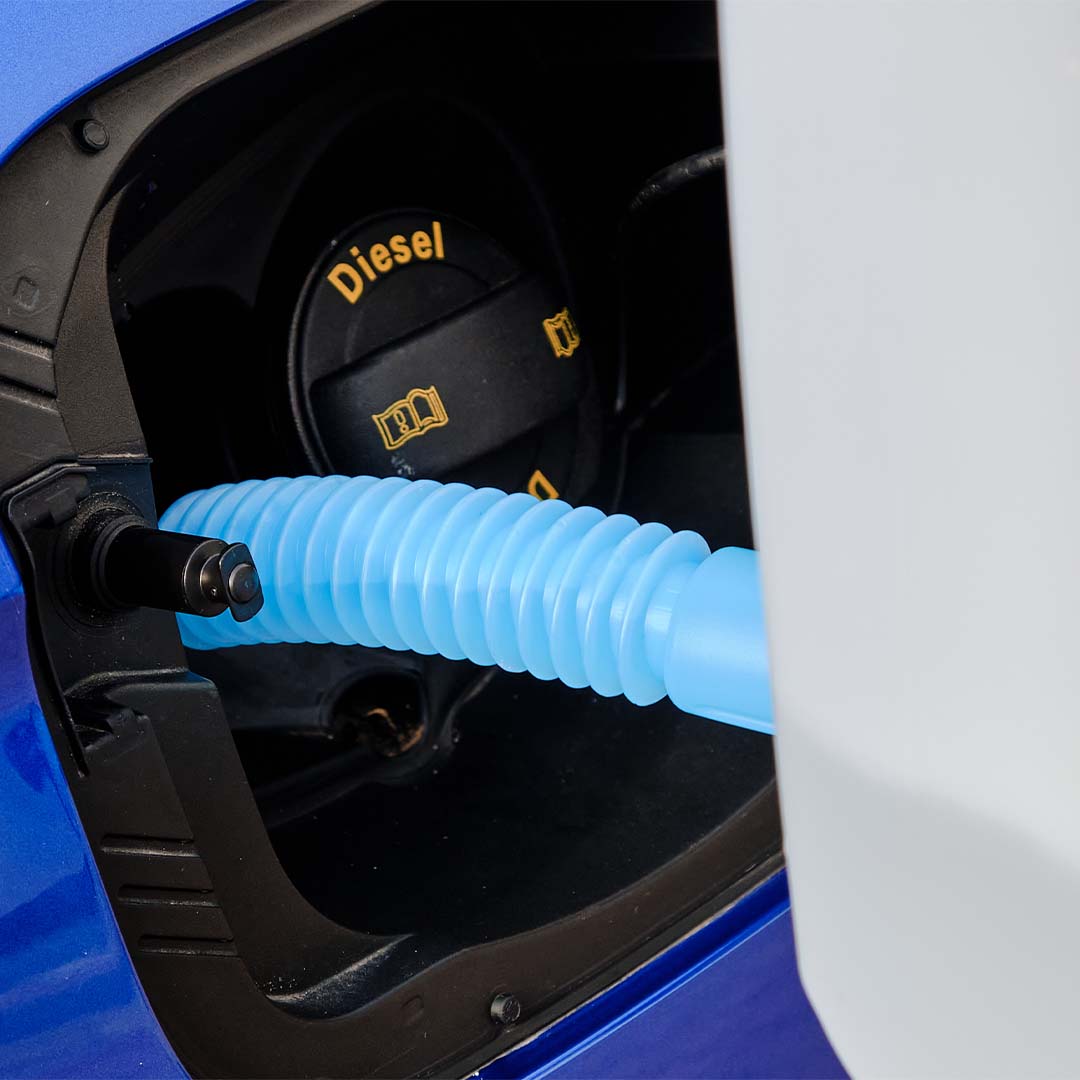
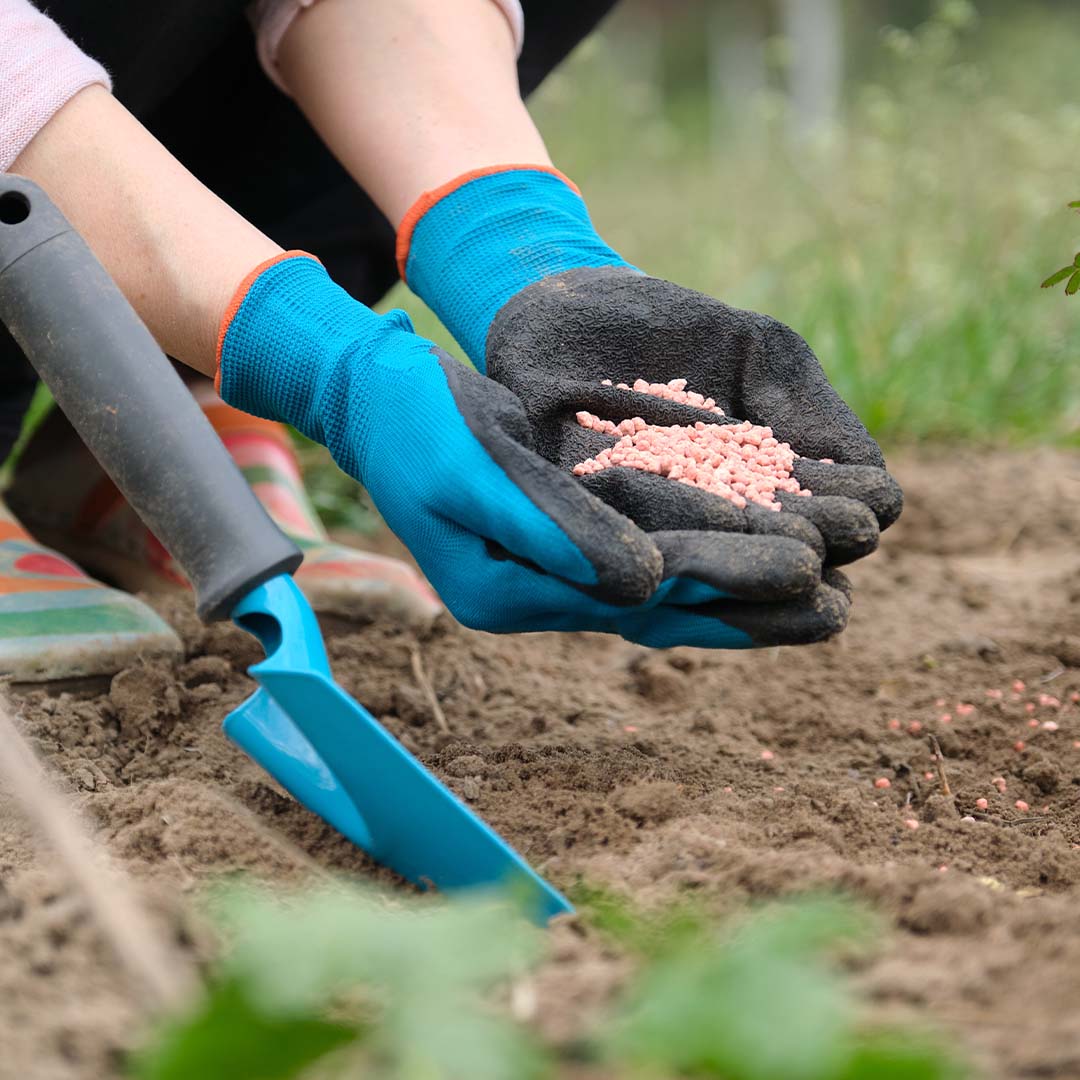
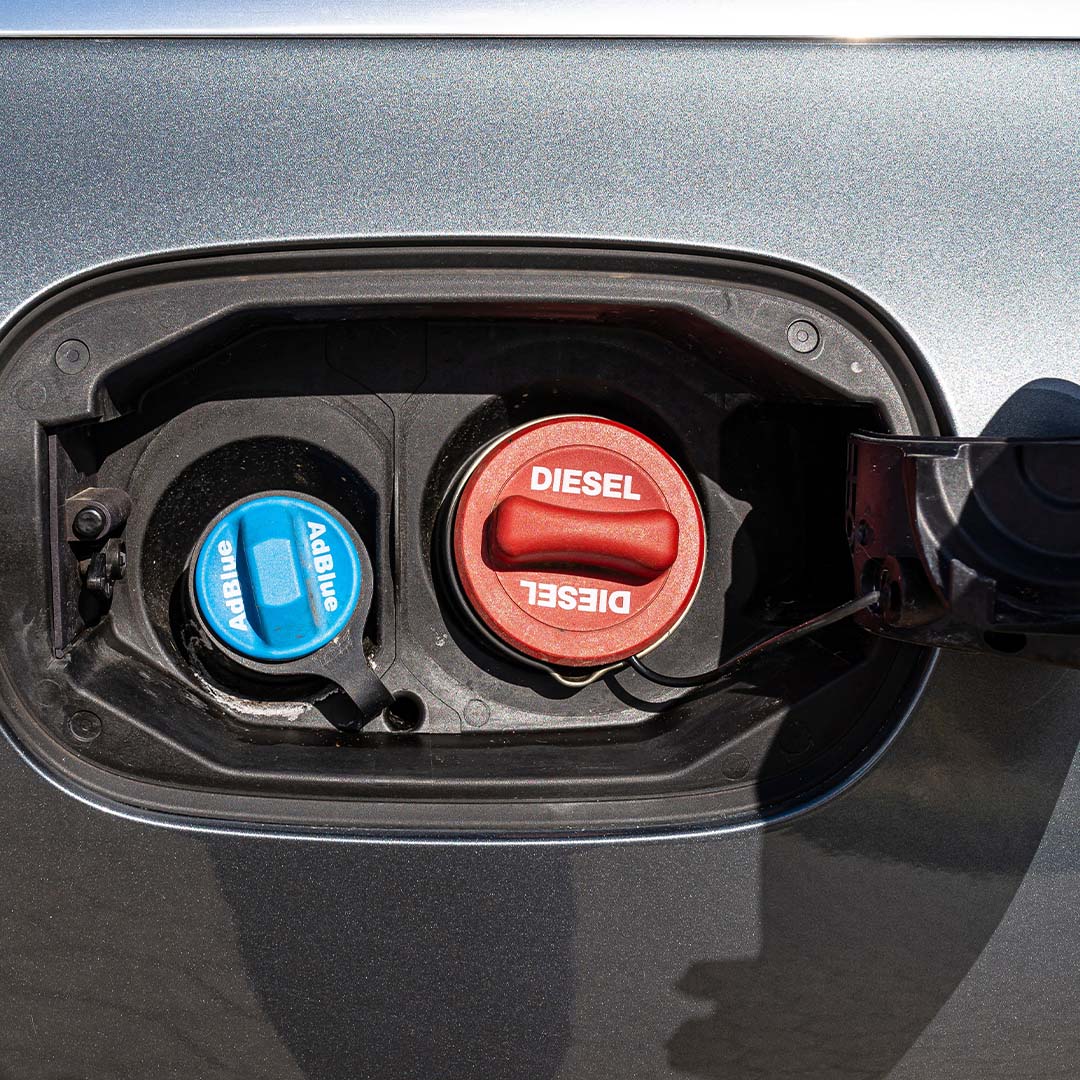
Objectives and Monitoring Parameters
The primary objective of the urea dilution process is to continuously monitor the concentration of urea during the dilution phase. This ensures that the concentration remains at the desired set point, maintaining product consistency and quality. The Maselli UR24 refractometer plays a pivotal role in this process, measuring the urea concentration in real-time in the production line and transmitting this data for process control. This in turn, adjusts the process as needed to maintain the optimal urea concentration.
Urea is industrially synthesized using the Bosch-Meiser urea process, which is based on the preparation of ammonium carbamate (H2N-COONH4) starting with liquid ammonia NH3 and carbon dioxide CO2, followed by decomposition of the ammonium carbamate into urea CO(NH2)2 and water. This process of synthesis, which takes place in a series of special high-pressure and high-temperature autoclave reactors (180 – 200 atm and 150 – 200°C), produces an aqueous urea solution at 60-70% which then undergoes various processes depending on the final use.
In most cases urea coming from the synthesis reactor, after being treated and filtered to remove any impurities, is thermally concentrated up to 2-5% of water and then taken to a solid state in subsequent stages which completely remove the water content by means of processes such as crystallization. Urea can be produced as crystals, prills, granules or flakes typically for use as fertilisers.
Alternatively, the aqueous urea solution in outlet from the reactors can be diluted up to a concentration of around 30 – 35% (usually the specific target is 32.5%), to obtain a final product which can be marketed in the automotive sector as an additive to reduce nitric oxide pollutants in exhaust gases produced both by industrial combustion processes and diesel-powered motor vehicles.
Understanding the Dilution Process for Automotive Applications
The urea dilution process is integral in transforming a concentrated aqueous urea solution into a final product known as “AdBlue,” used as an additive in the automotive industry. AdBlue is a diesel exhaust fluid used in vehicles with Selective Catalytic Reduction (SCR) technology to reduce harmful gases being released into the atmosphere. AdBlue is a 32,5 % solution, synthetically manufactured high purity urea in de-mineralized water. The process begins with liquid urea at a concentration of 60-70%, mixed with demineralized water. The final product is a diluted urea solution with a concentration of 30-35%. This process is crucial for producing a product that helps reduce nitric oxide pollutants in exhaust gases.
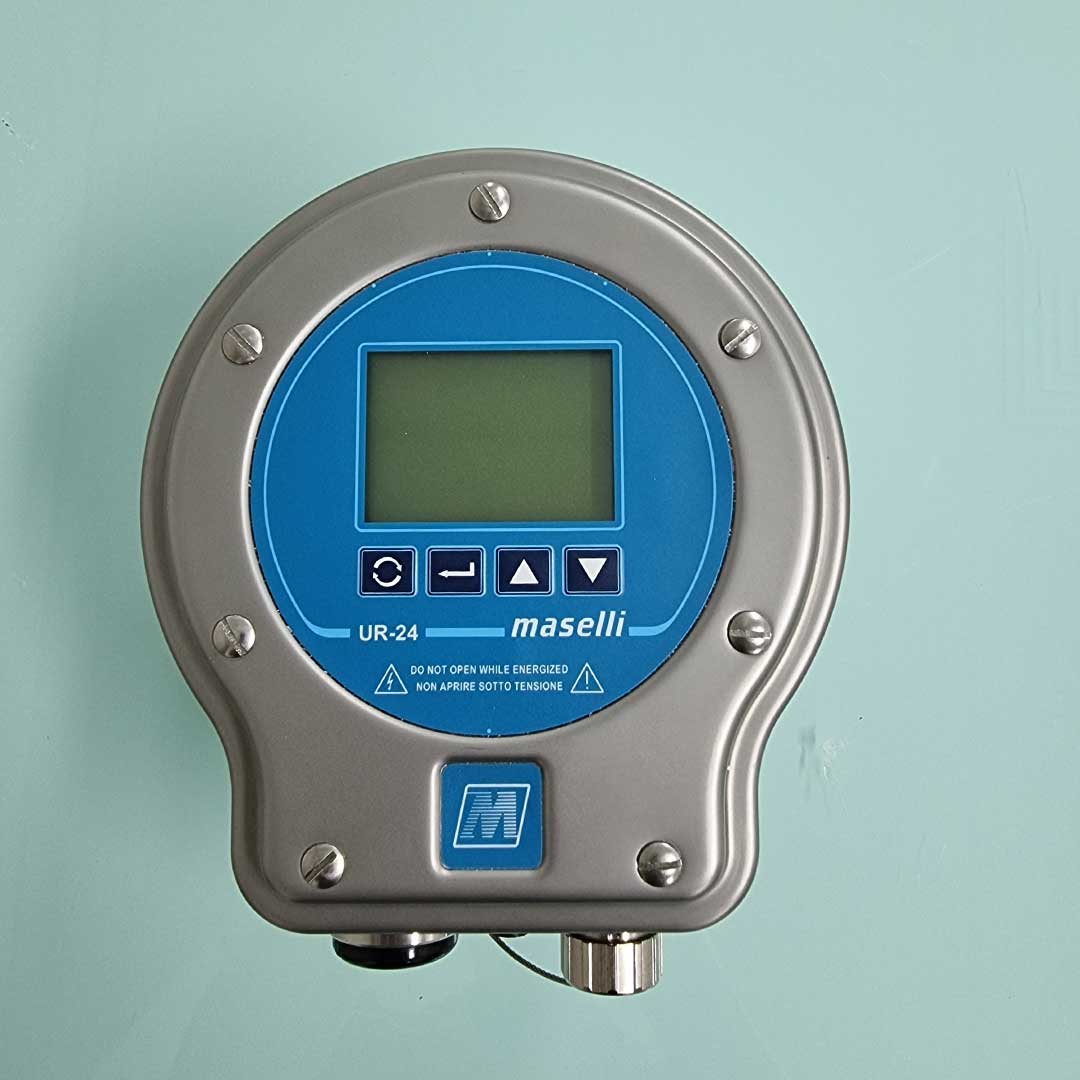
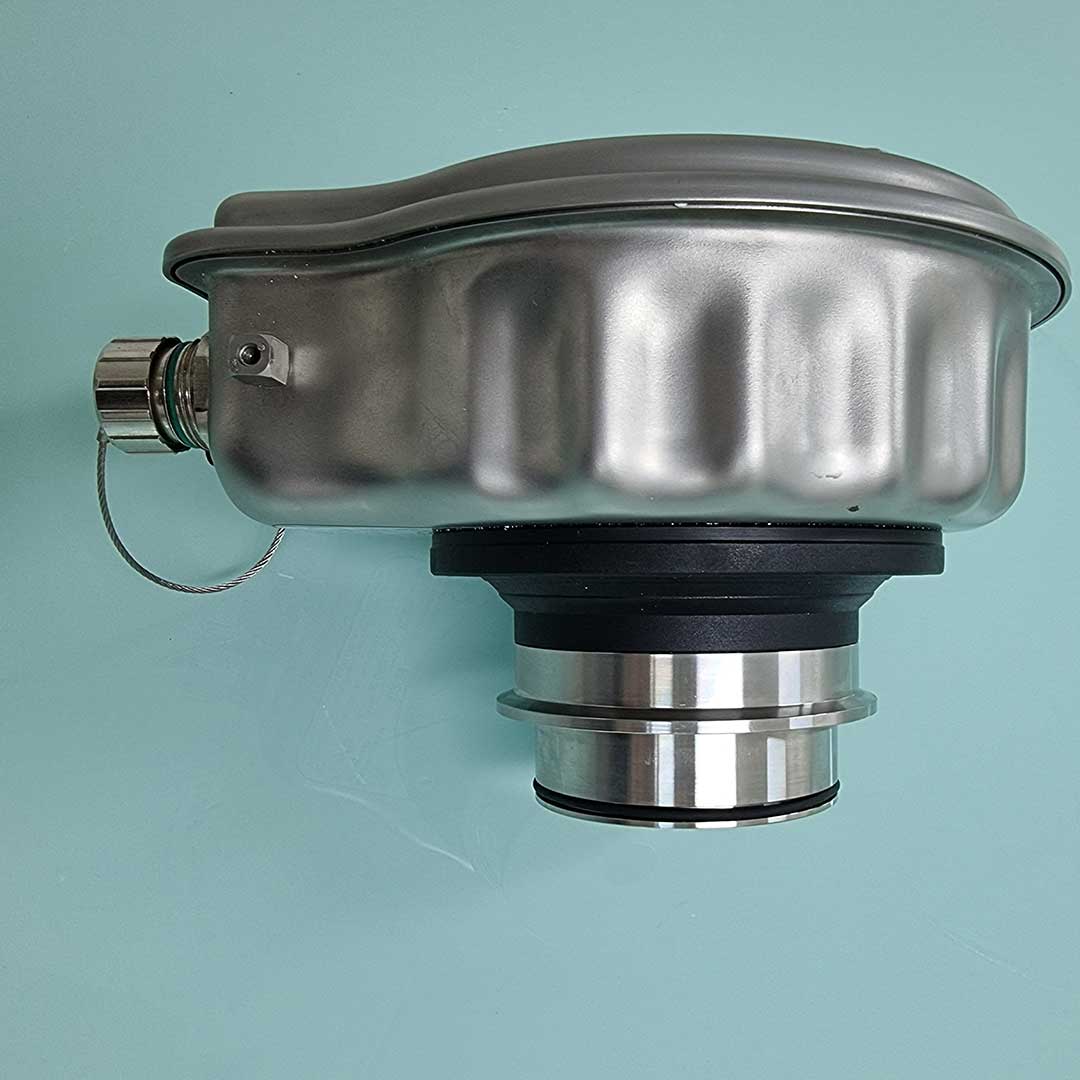
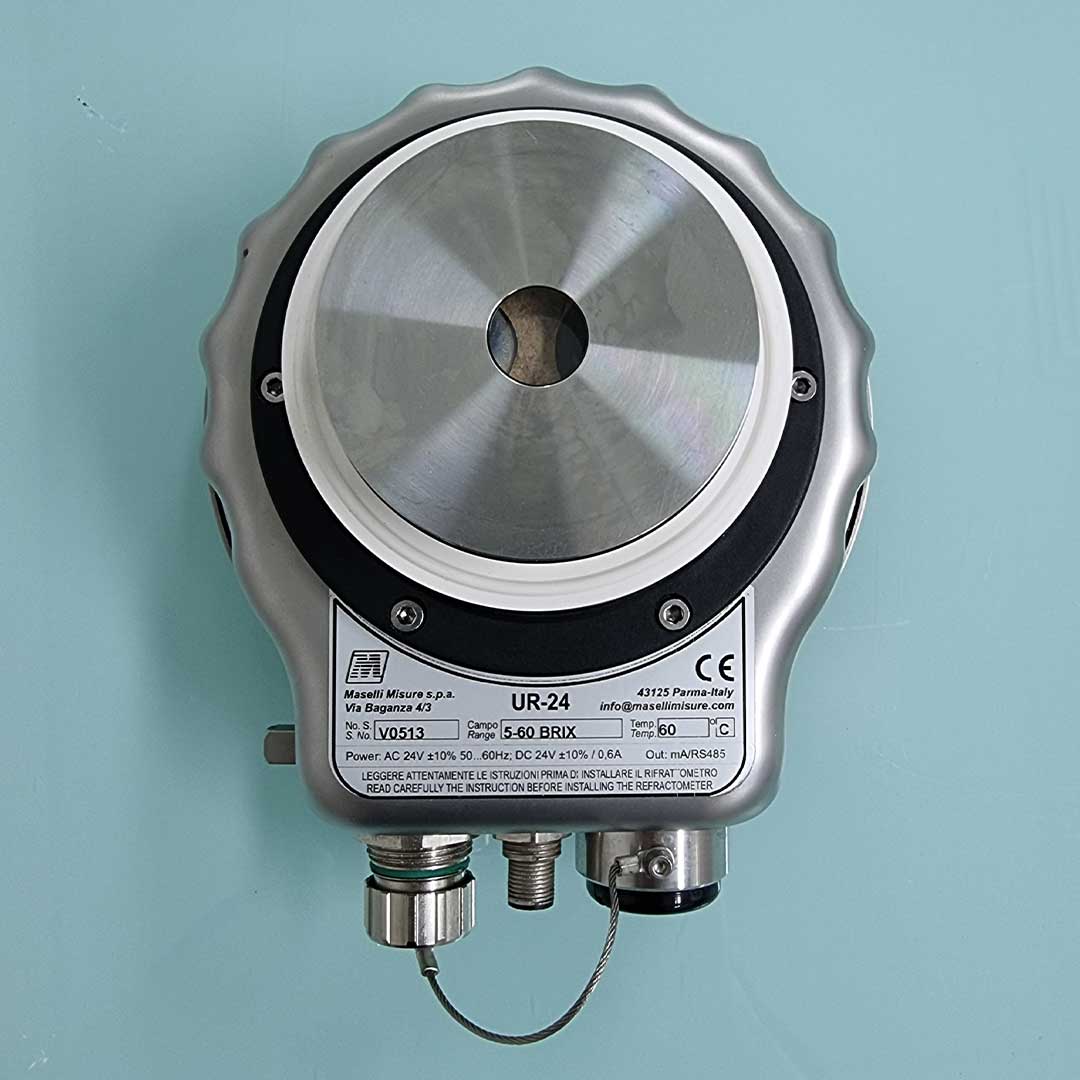
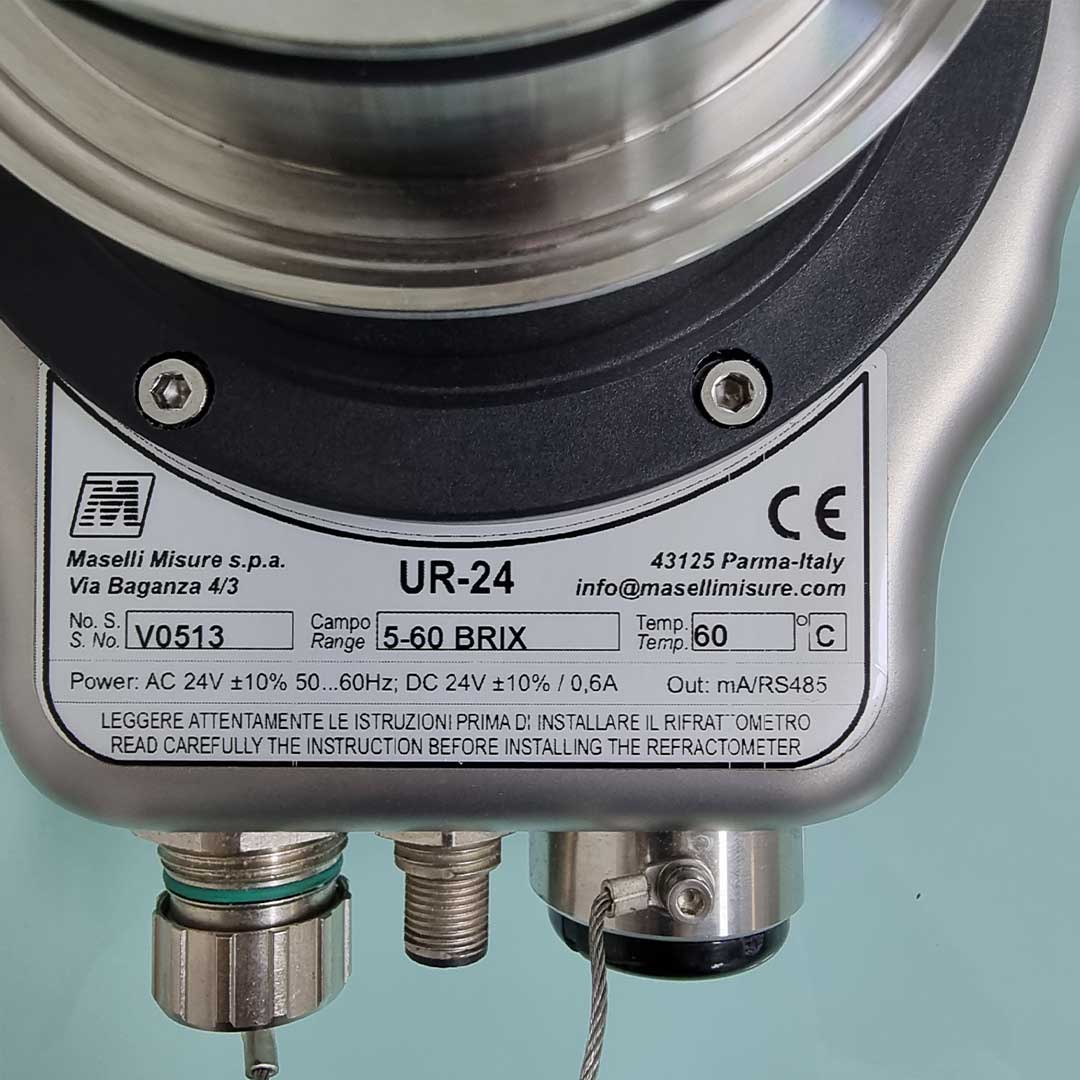
Plant Layout and Installation Points
The plant layout for urea dilution varies based on the technology used, with batch and continuous processes being the most common. The Maselli refractometer unit, essential for monitoring urea concentration, is installed at strategic points in the system to ensure accurate and reliable readings. These installation points are critical for the successful operation and monitoring of the urea dilution process. Typically for a Urea concentration measurement the Maselli UR24 is in the recirculation line to the mixing tank. In the case of mixing via a static mixer the UR24 refractometer would be placed in the line after the mixer for feedback control to the water addition.
Automation in Urea Dilution
Automation plays a vital role in optimizing the urea dilution process either by a mixing tank or static mixer. In a typical batch system, a Programmable Logic Controller (PLC) controls the addition of key ingredients like concentrated urea and water and monitors the final urea concentration in real-time. This automation ensures precision in the process, leading to a consistent and high-quality final product and increased product yeild. The PLC adjusts the process parameters and makes the process fully automated, based on real-time data from the Maselli refractometer unit.
Economic and Technological Benefits
The integration of the Maselli refractometer unit and automation in the urea dilution process brings about significant economic and technological benefits. These benefits include optimized operating conditions, reduced energy consumption, and lower management costs. Additionally, the process ensures a consistent product quality, aligning with industry specifications and standards.
Comparison with Other Solutions
When compared to other solutions and methodologies, the use of the Maselli refractometer unit and automation in urea dilution stands out for its efficiency and reliability. This system reduces the need for labour-intensive monitoring and adjustments, leading to cost savings and improved process efficiency. The refractometer being a primary standard in analysis also provides a far more accurate concentration analysis than other secondary technologies.
Summary
Urea also presents itself as an odorless crystalline solid used as fertilizer which is widely used thanks to its high titer of nitrogen it is also used for zootechnical applications where it is added to feed for ruminants whose microorganisms convert it into bacterial protein. Urea is also a critical component in the production of additives for the automotive industry.
The integration of the Maselli UR24 refractometer and automation of the urea process ensures a consistent and high-quality product. The economic and technological benefits of this system underscore its significance, paving the way for future advancements and optimizations in the field.