Carbon Dioxide (CO2) dissolution technology
Molecular Processing Solutions “SubCarb” redefines the concept of beverage carbonation by its revolutionary patented technology for water and CSD carbonation at the molecular level.
Setting a new industry standard for beverage carbonation systems by improving the efficiency and effectiveness of CO2 carbonation, with energy and quality benefits
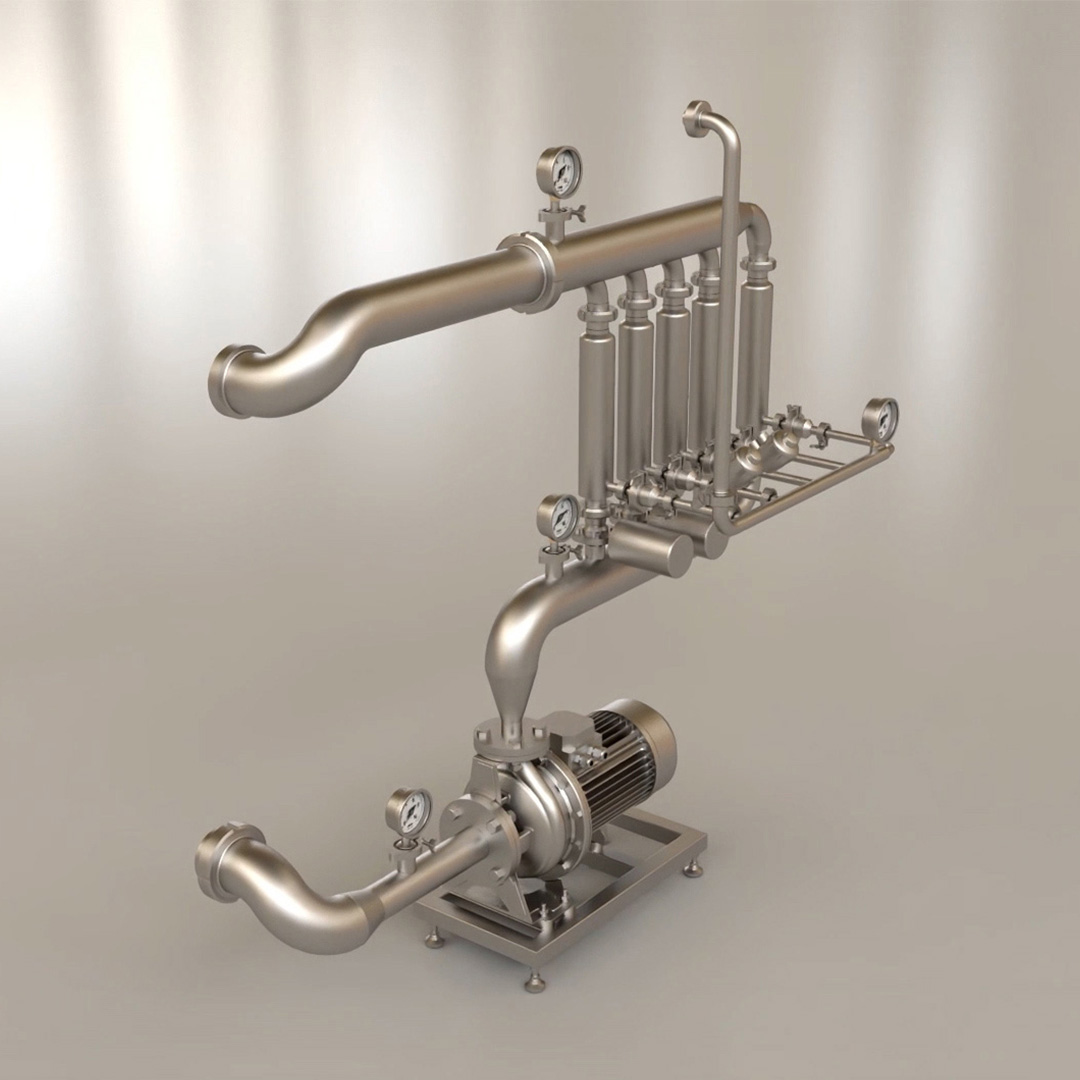
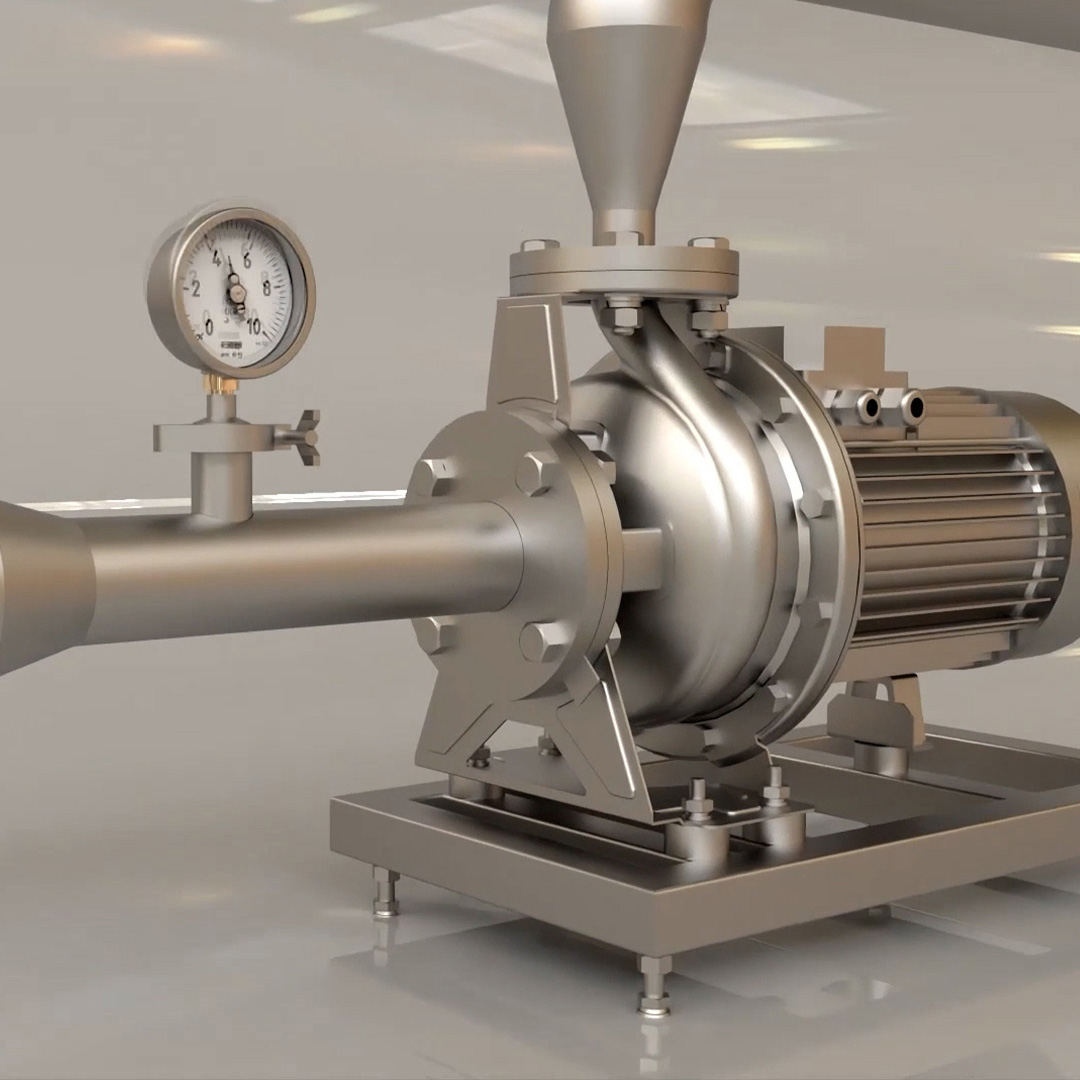
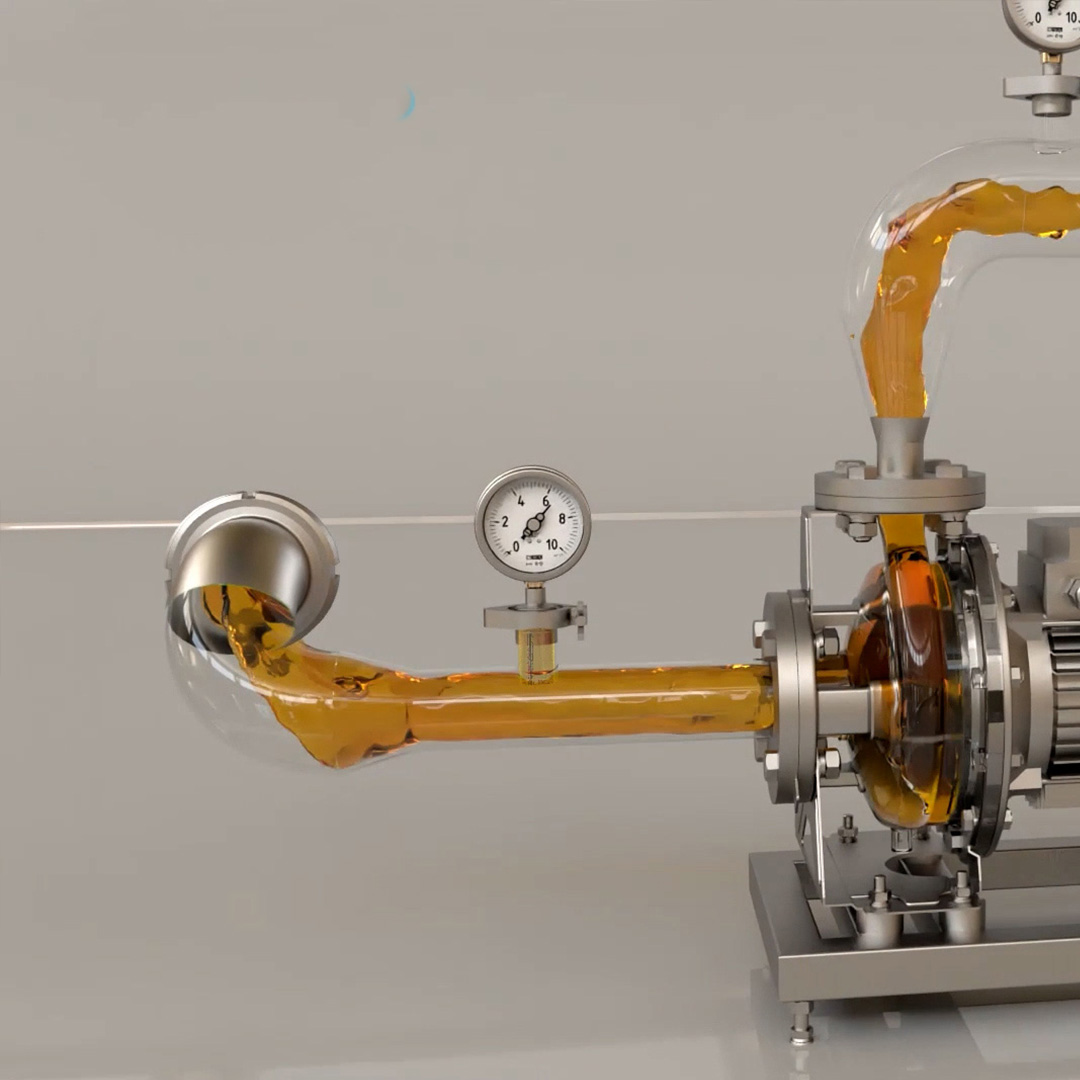
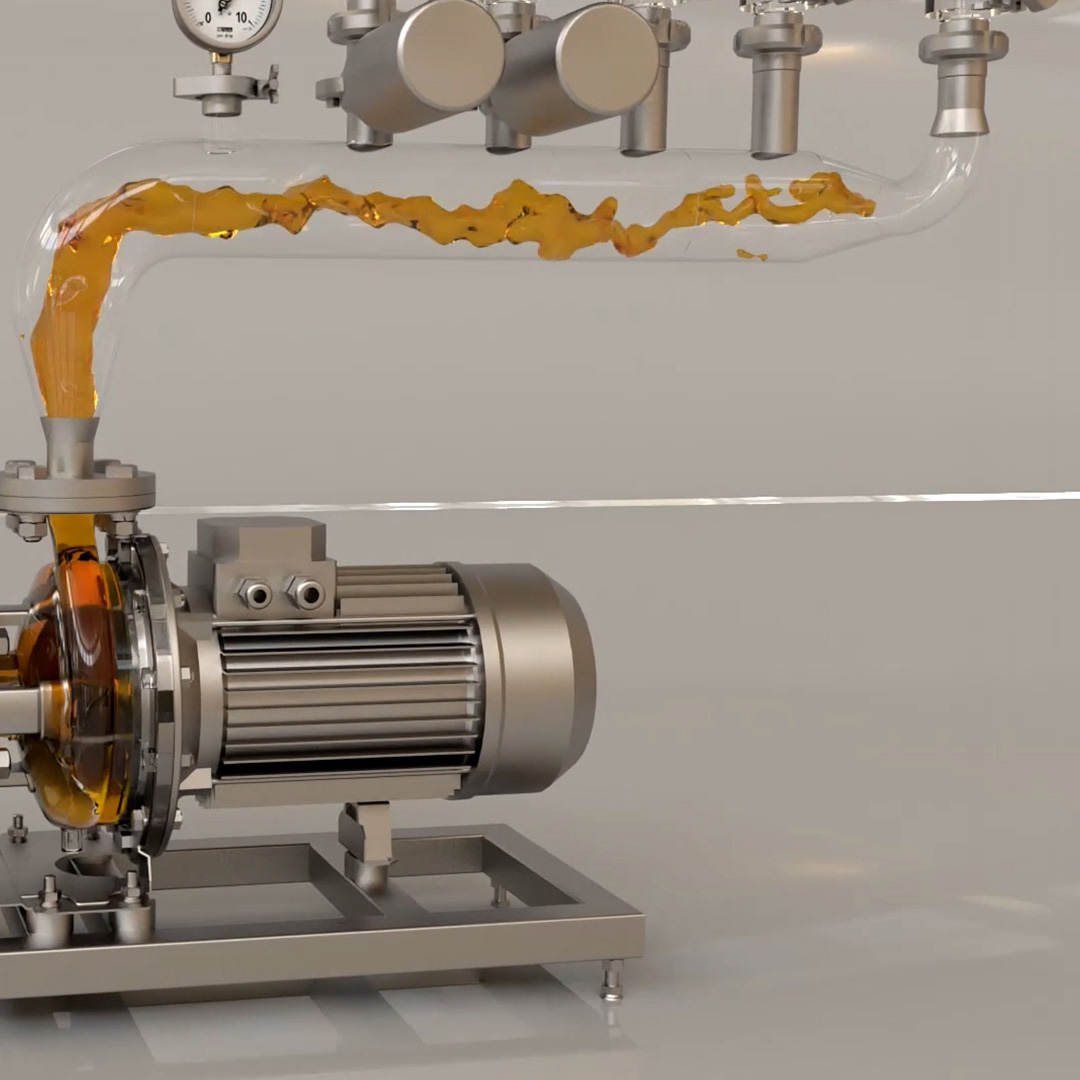
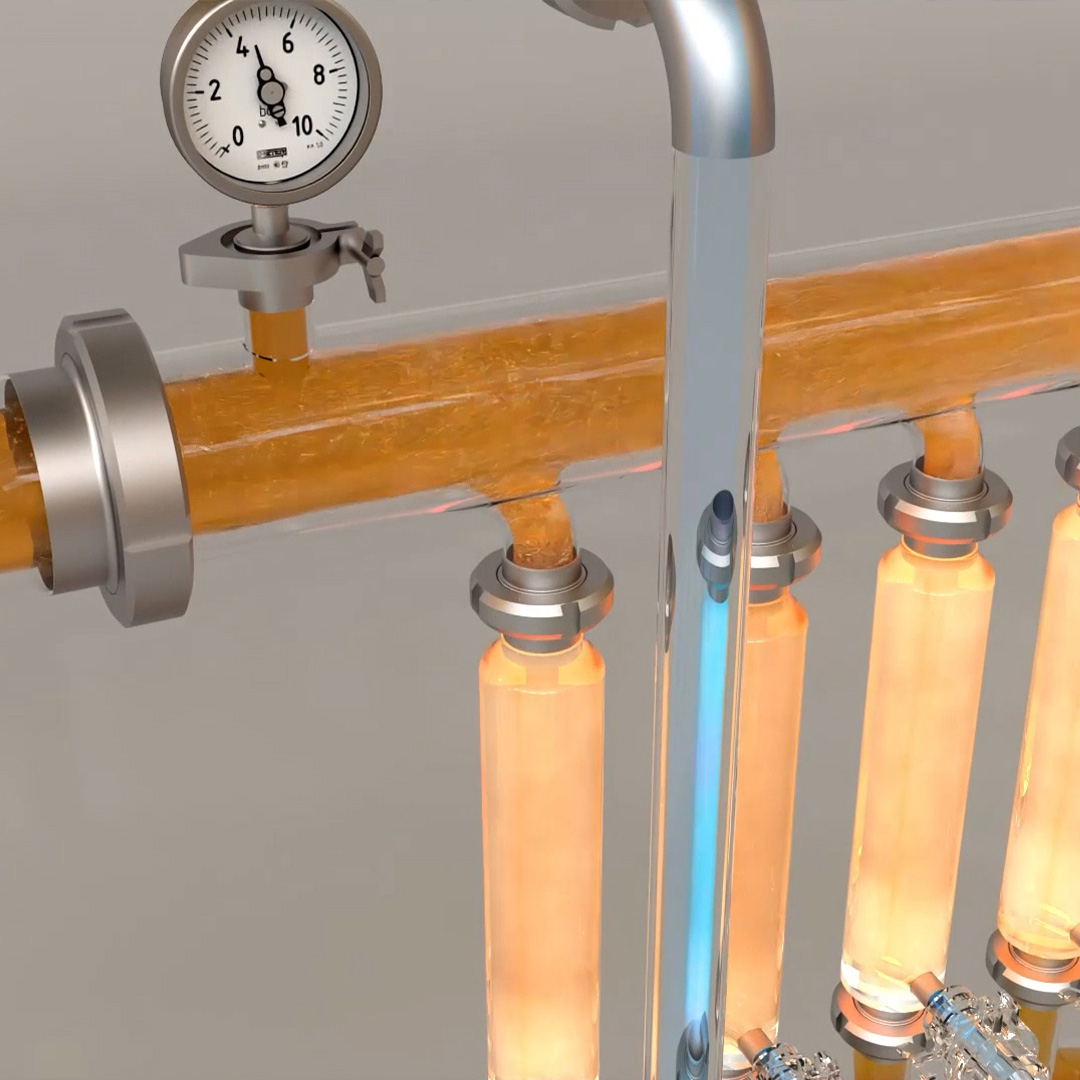
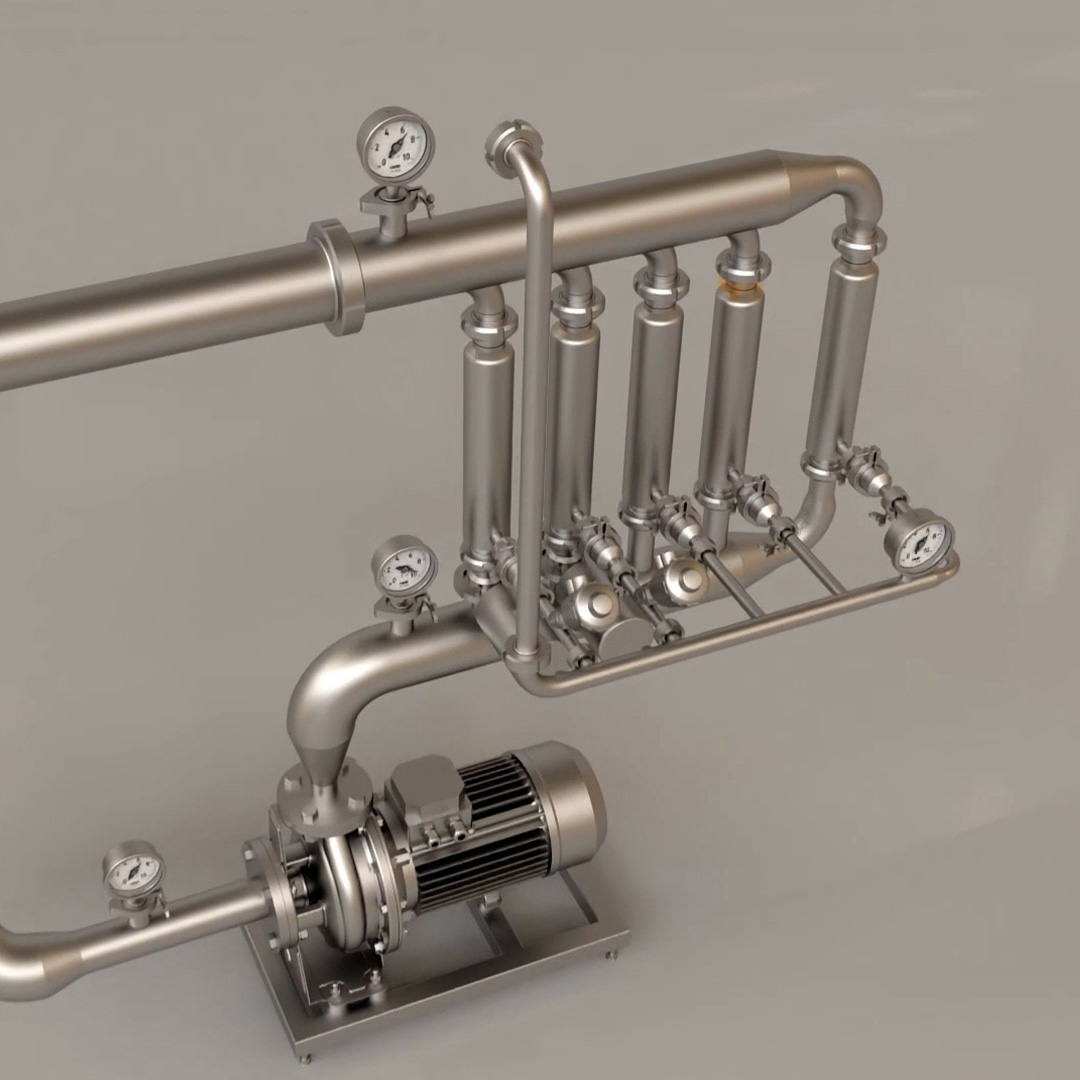
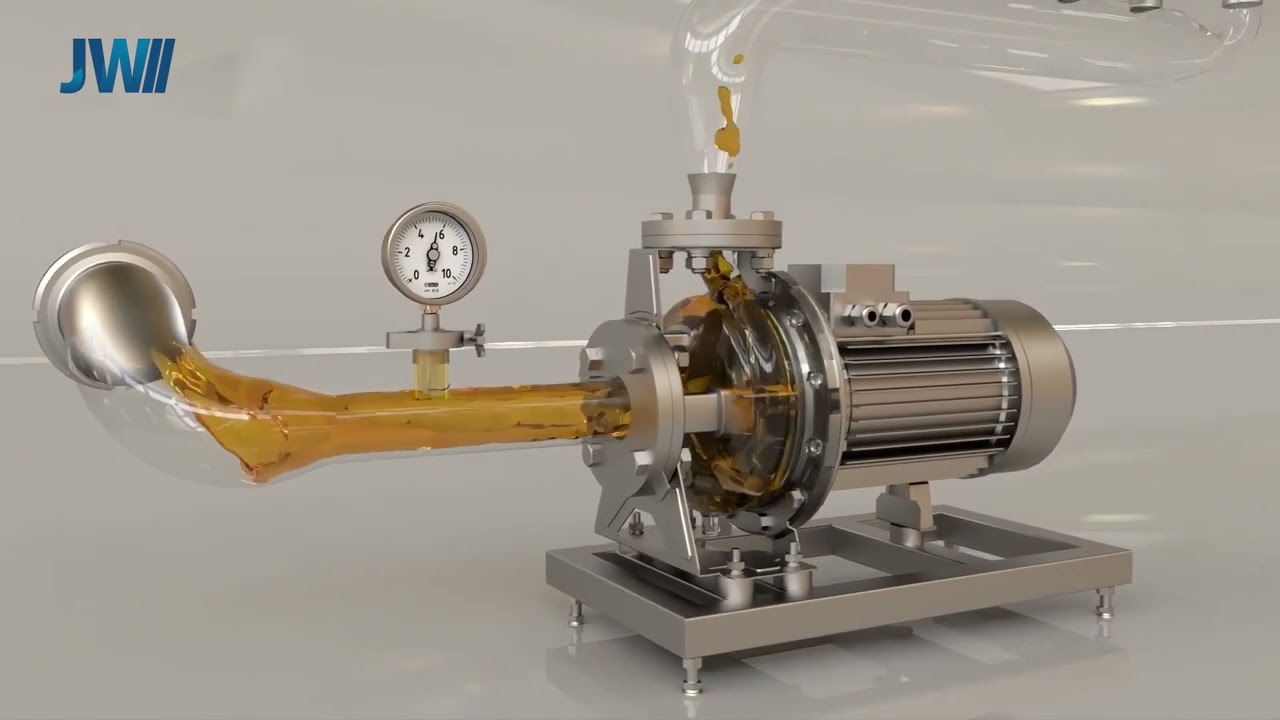
SubCarb system implementation
The SubCarb system can be retrofitted to existing carbonators, the upgrade is simple with minimal downtime and has been proven on all the major carbonator brands globally. The system is also used and proven by a wide range of clients from large multinationals to smaller scale bottlers.
Sustainability benefits
The technology is helping the industry with more efficient carbonation of soft drinks at higher temperatures. If you can carbonate at a higher temperature you have energy savings as you do not need to chill the liquid to get optimal carbonation and you also do not need to warm the package again to add a label or pack it, you also avoid condensation so air knives can be turned off which saves compressed air. Overall the system provides improved efficiency and effectiveness.
Traditional CO2 Dissolution
To improve dissolution of CO2 in liquids traditionally there are 2 methods currently used: you can increase partial pressure or cool down a liquid. These actions are very costly and impact the bottom-line.
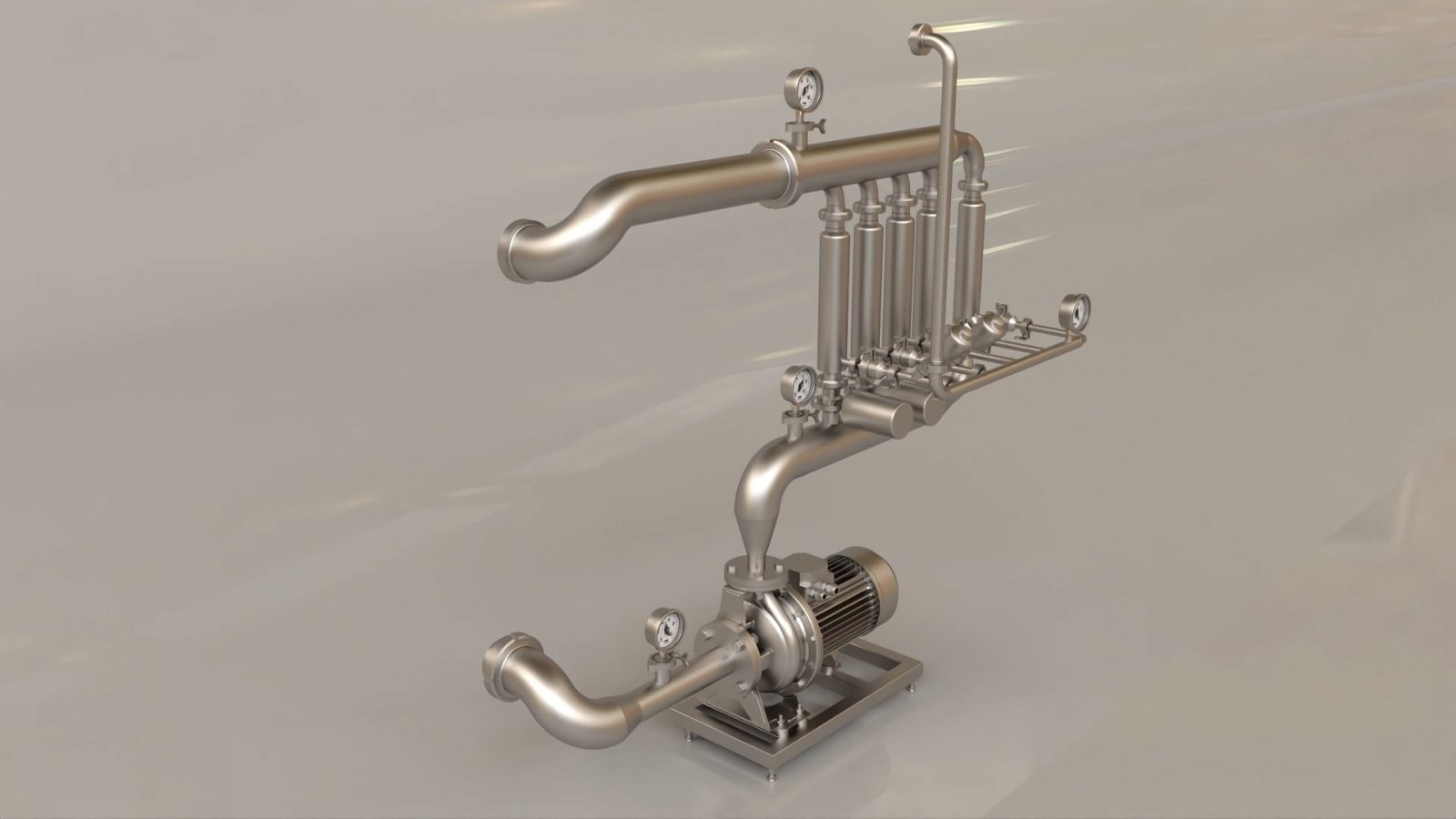
Increasing the surface of mass transfer
Molecular Processing Solutions technology works on the principle of increasing the surface of mass transfer between the mixing ingredients: liquid and gas. This is a breakthrough innovation in the field of beverage carbonation with installations globally at major beverage brands the technology is proven and has a fast return on investment. JWII are pleased to be able to offer this technology to our clients in Australia and New Zealand.
Good and bad Carbonation
The molecular structure of water is like a sponge, poor CO2 dissolution is where the outer layer of water is carbonated and not the core. Good CO2 dissolution is where the whole volume is uniformly carbonated.
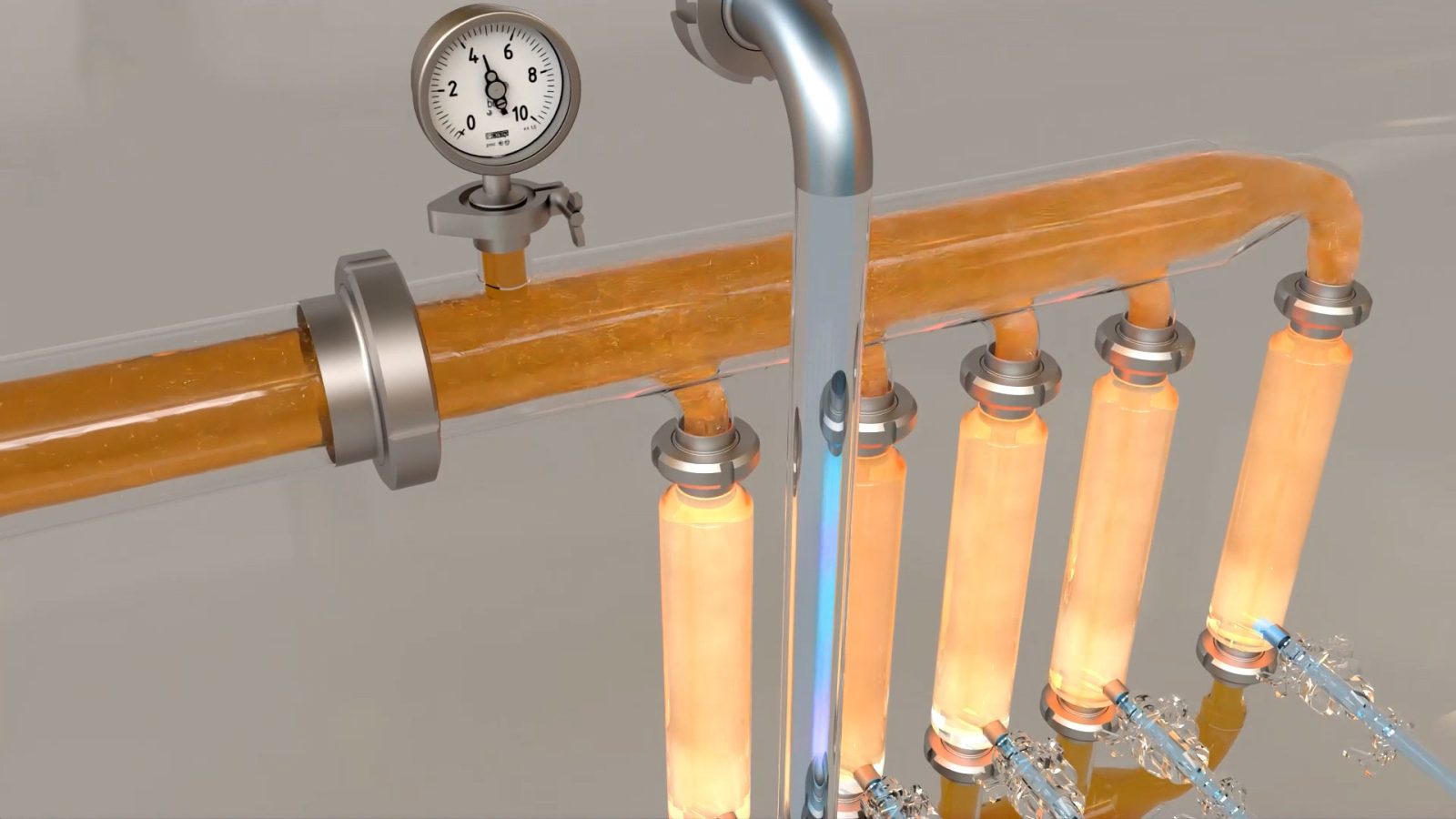
Carbonation Technologies and devices
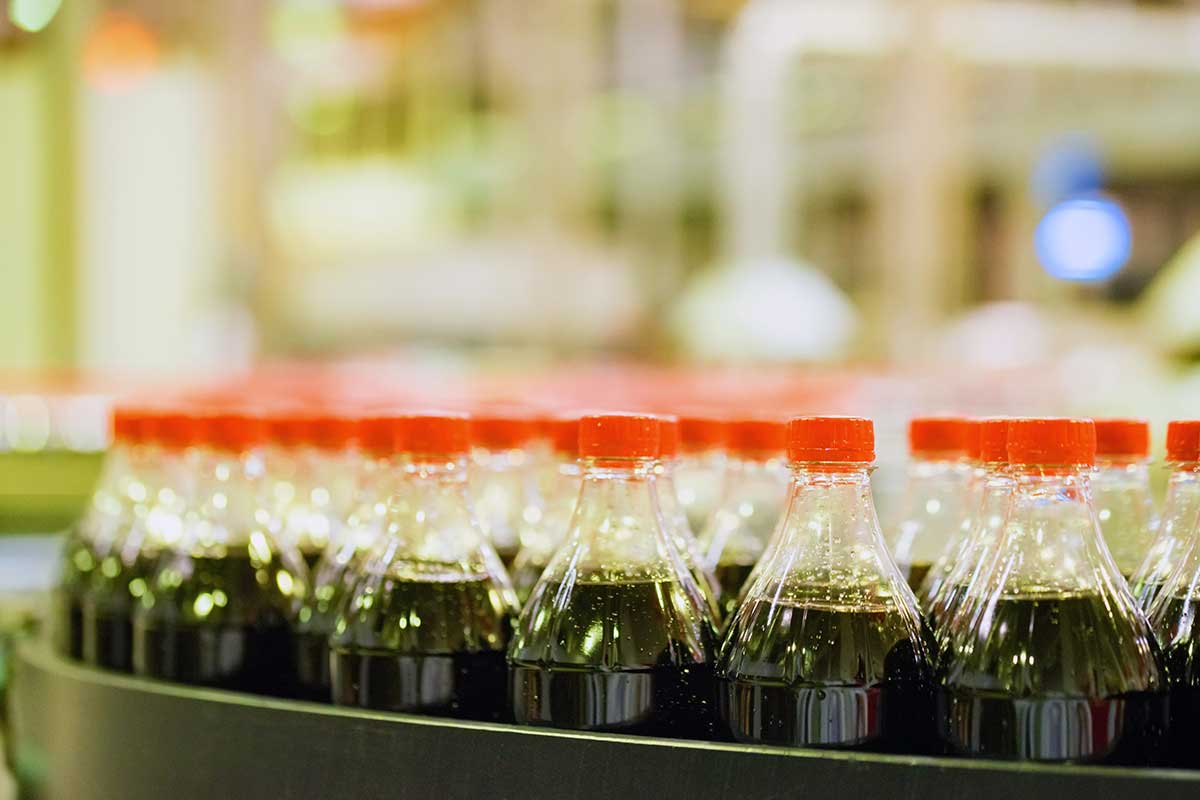
Patented technology from Molecular Processing Solutions
Our patented system is designed to achieve the greatest degree of turbulence at supersonic speeds and the lowest physically possible pressure drop. The technology aims to achieve the effect of “cold boiling” (boiling without heat). When liquid changes to a vapor for a few milliseconds and then immediately condenses at ambient the CO2 absorption is significantly improved when the vaour is mixed with CO2 gas.
SubCarb technology
Liquid in the form of water of non carbonated beverage is changed to the aggregate state to become gaseous. CO2 gas is mixed with the vapour which ensures bonding at the molecular level with the surface of mass transfer 10,000 times greater than existing technologies. The effectiveness of carbonation reached physical maximum ensuring CO2 dissolution with more than 97% efficiency.
Sustainability benefits through energy savings
CO2 bonding using the SubCarb technology can operate at high temperatures upto 23C and in many cases lower carbonation pressure. This provides significant sustainability benefits in electricity and CO2 savings. This helps with fast return on investment once the technology is implemented.
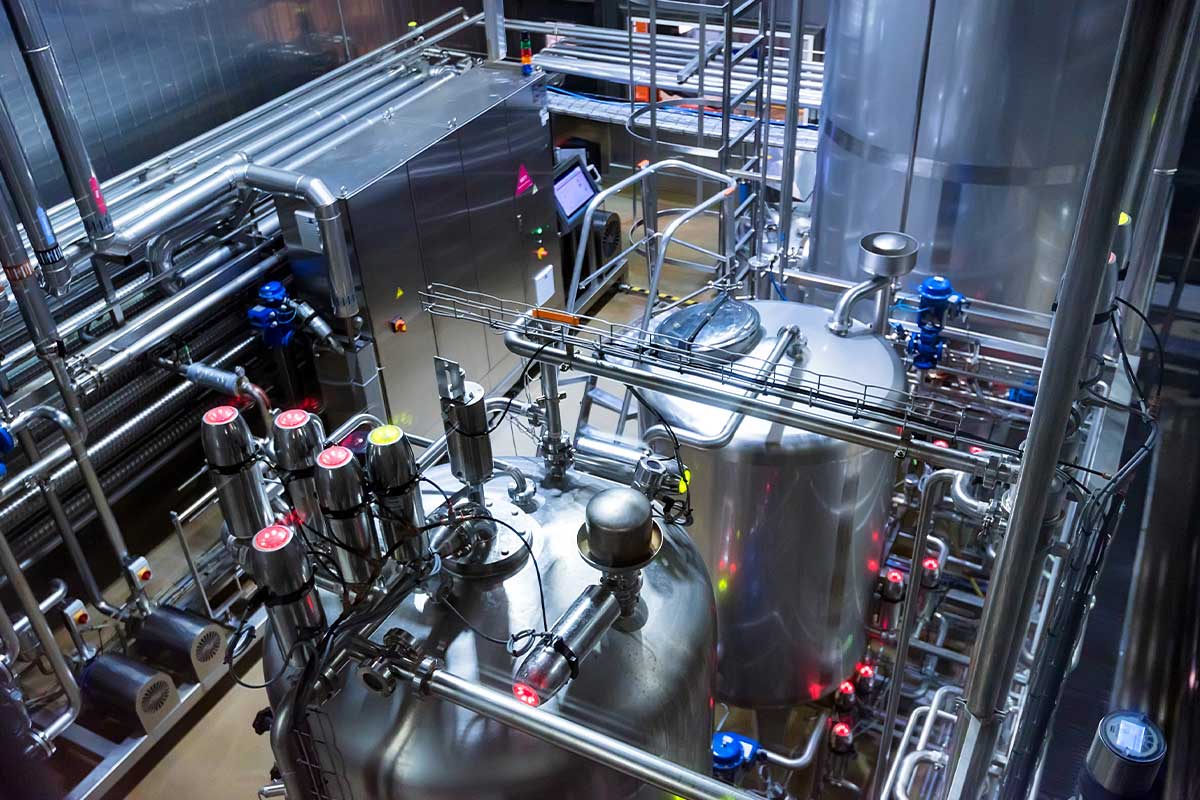
Eliminate Foaming issues
Using CO2 bonding technology like SubCarb not only provides energy benefits it also reduces product foaming, which is especially problematic on non-sugared diet products. Beverages carbonated with our technology reduces foaming by 2 to 2.5 times, this leads to yield benefits with syrup and better retention of CO2 in the product. This also helps to contribute to the system payback.
Dissolved CO2 stability and retention
When product quality is the main driver it is important to ensure the carbonated beverage actually stays carbonated throughout the supply chain cycle and once opened. SubCarb helps improve CO2 retention and stability and that has been reported by clients with new and old carbonation equipment.
Eliminate Condensate
One of the key issues with existing carbonation systems is that the liquid must be chilled to get carbonation effectiveness causing condensation. Using MSP Subcarb you can eliminate condensation, so that labels can be applied, pallets do not leak and fall apart, air knives can be turned off saving on compressed air as the bottles can be filled at ambient temperature with no condensation.
Can processing and higher savings
On a typical CSD can line the product is chilled to carbonate then the cans have to be sent through a heat tunnel warmer before they can be packed. This is to avoid condensation and the package becoming damaged. Using SubCarb the liquid does not need to be chilled therefore eliminating the need for the can warmer.
Upgrade existing systems
The SubCarb technology is a system upgrade to existing lines and with over 400 upgrades with over a hundred different bottlers in the industry MSP SubCarb is a proven technology globally. If you are thinking of investing in a new chiller, don’t, this technology is far easier to apply and will have payback in a very short period of time. JWII are able to provide existing case studies and references of the system benefits and savings so please contact us today for more information on this revolutionary technology now available to the Australian and New Zealand Carbonated beverage Industry.
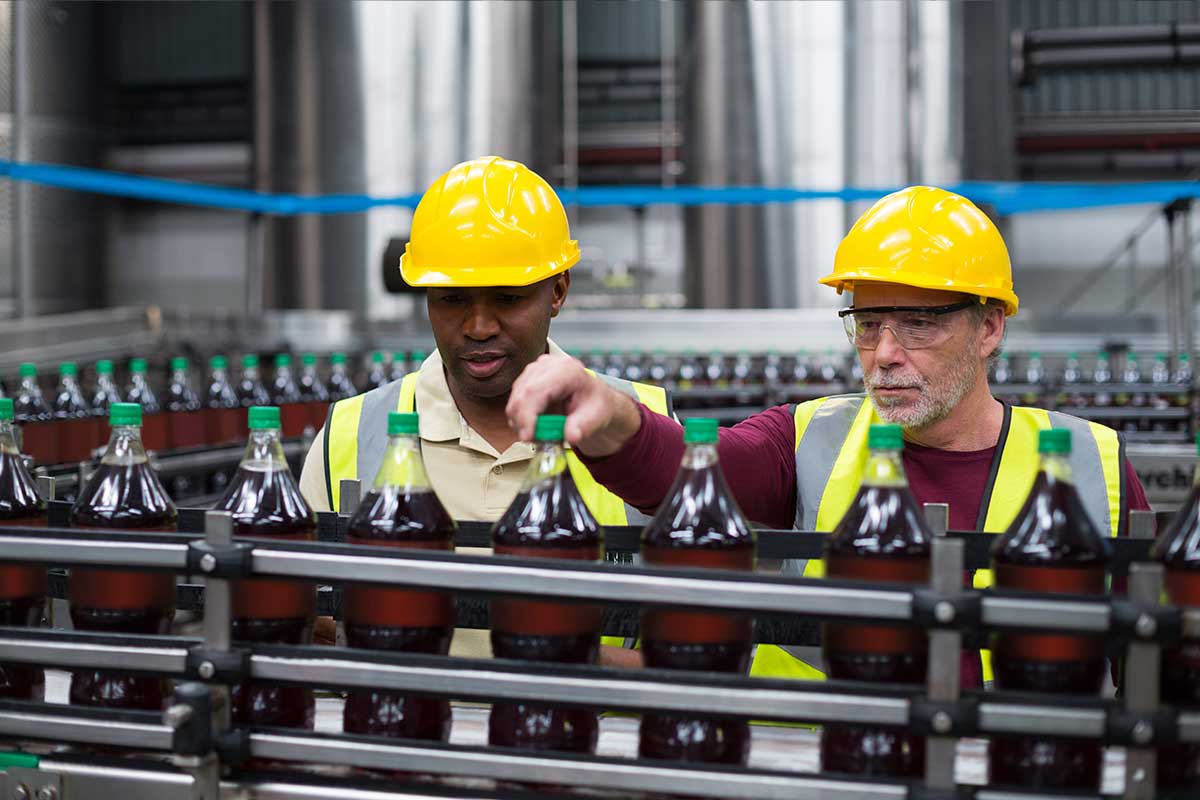
- CO2 Injection Technology
- CO2 injection in beverages
- CO2 Dissolution
- Carbon Dioxide injector
- Carbon Dioxide dissolver
- Beverage carbonator
- Soft drink carbonator
- Carbonator machine
- Beverage carbonation system & supplies
- Commercial carbonation machine
- Industrial carbonation machine
- Beverage carbonation systems and supplies
CO2 Dissolution Questions answered by our experts
How is CO2 dissolved in beverages?
This is normally achieved by using a saturator where the CO2 is forced under pressure into a tank containing the liquid. Other methods for dissolving CO2 are direct injection using nozzles to directly inject the CO2 into the product.
Why is CO2 Dissolved in soft drinks?
CO2 is an odorless gas and is used to enhance the flavor and feeling of the beverage for the consumer. Different beverage styles have various carbonation levels and the amount of CO2 used will be determined by the bottler during the R&D phase for the beverage flavour.
What happens to Carbon Dioxide in drinks?
The CO2 dissolves into the liquid and these CO2 many people like the sensation of these bubbles bursting on the tongue as the beverage is consumed.
What temperature does CO2 absorb efficiently in liquid?
Typically the beverage is chilled to below 5C to obtain efficient dissolution of CO2 into solution, and this is the industry standard method currently. This means the liquid must be chilled using a lot of energy to reach this temperature. Technologies like the SubCarb allow dissolution at ambient temperature and therefore the same carbonation efficiency can be achieved with dramatic energy savings.
Is Dissolved CO2 an ingredient?
Once CO2 is dissolved into a consumable beverage manufacturers typically regard it as an ingredient. It is therefore important the CO2 used is pure without contamination. The beverage industry uses guidelines put out by the International Society for Beverage Technology (www.isbt.com). Industry have technologies in place to adhere to these industry standards for CO2 purity.