An Evolving Beverage Industry
In the rapidly evolving beverage industry, precision and efficiency in production are key. Maselli offers two state-of-the-art solutions – the IB08 and IB07 beverage analyzers – each designed to meet different needs within the industry. Understanding these analyzers can help you choose the right one for your production line.What is a Beverage Analyser?
Inline Beverage analysers are sophisticated, real-time monitoring systems used in the beverage industry for process and quality control. These analysers can handle a wide range of beverages, including carbonated drinks, juices, dairy, kombucha, plant-based drinks, diet beverages, and alcoholic beverages. Key parameters measured by these systems include refractive index, Brix, % Diet, oxygen, carbon dioxide, pH, and conductivity. These typically offer a modular system design, allowing users to choose specific analytical modules based on their needs. These systems are designed for robust, maintenance-free operation and come equipped with user-friendly controllers for efficient data management and process control.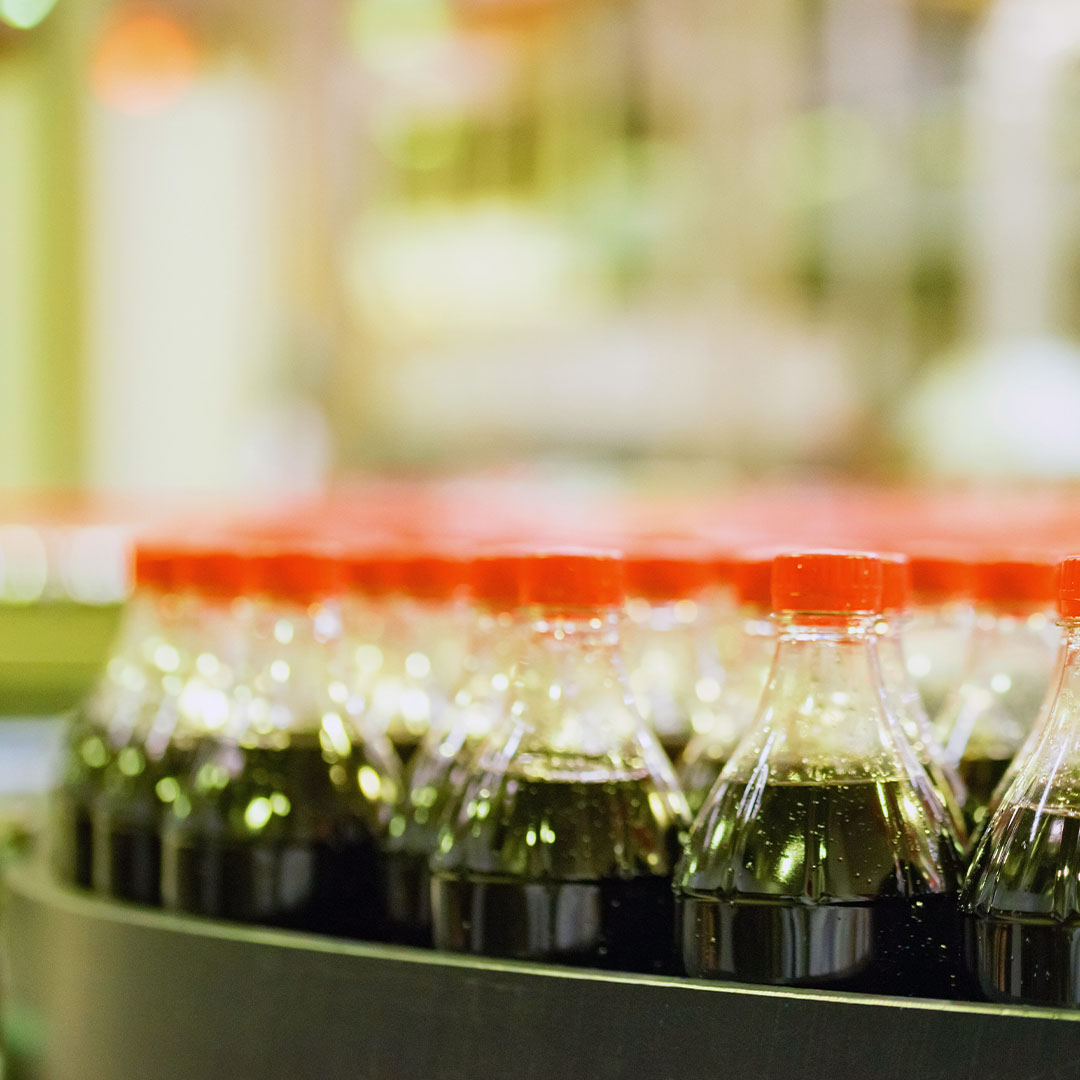
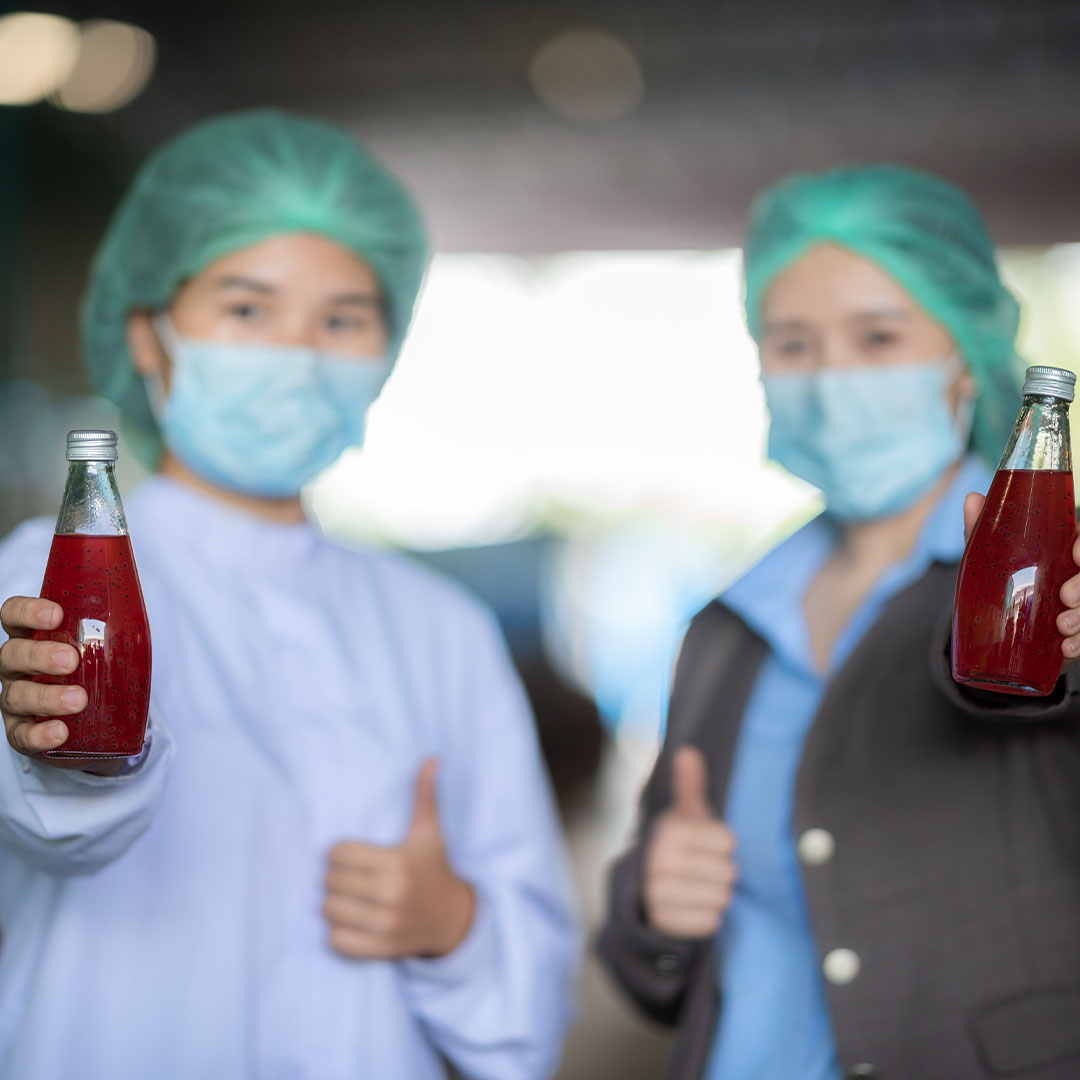
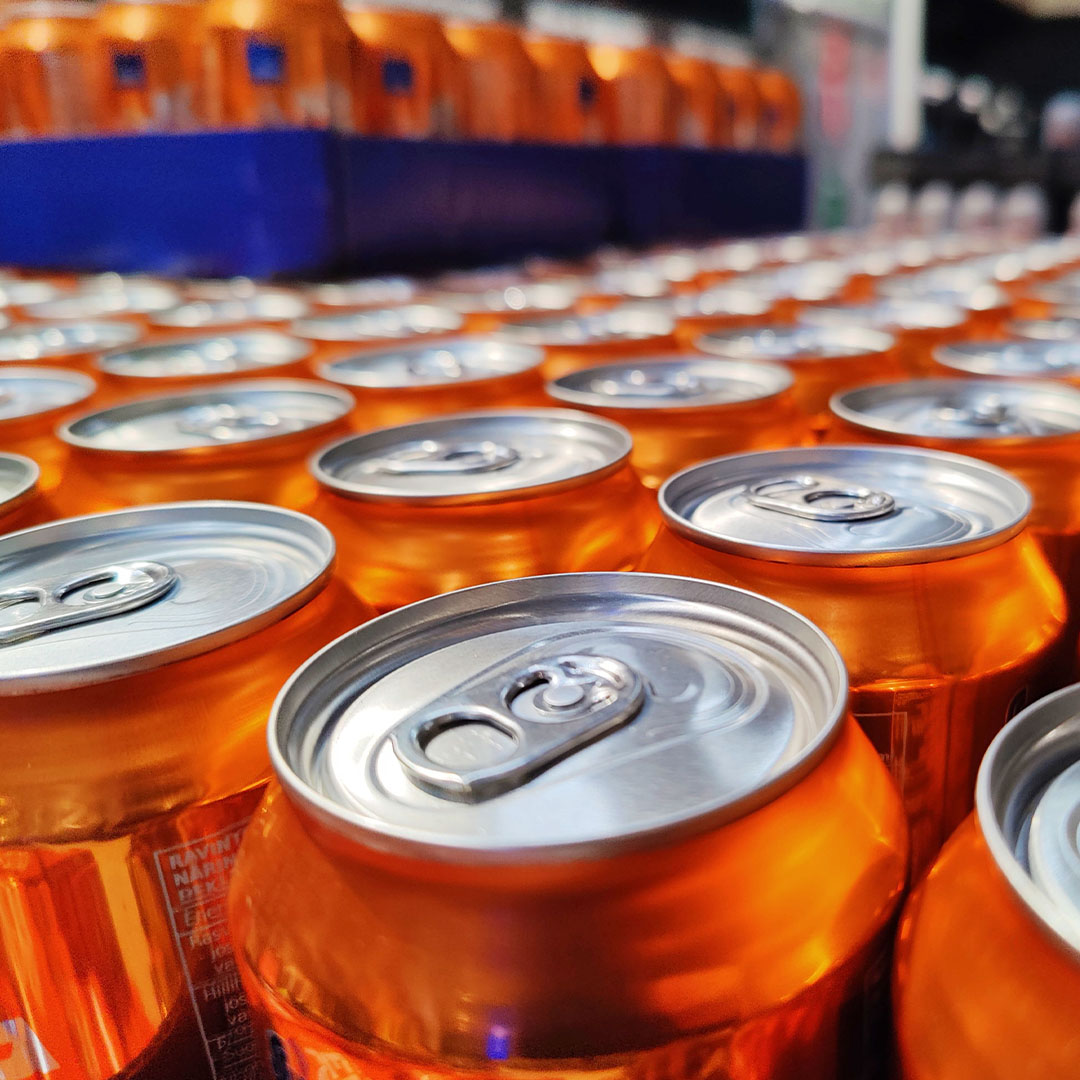
How can a Beverage Analyser be used?
If we look at how beverage monitors are used, we can see that the industry uses them in 2 specific ways. To be able to select the correct type it is very important to establish what is the purpose of the installation, and what is the client wanting to achieve by using such a device to oversee the process. Typical ways to use this equipment are:
- Option A – You simply want an in line monitor to alarm when measuring out of product specification This is using the device more like a monitor, to alert the plant personnel of an issue. In this configuration the beverage analyser can be installed directly in line either after the last tank or directly in the line to the filing machine. This way if there is an incident where the condition of the beverage is out of specification an alarm or beacon can be used to let the plant operator the process needs to be adjusted to bring the product back to the target range. The analyser could also be connected to stop the line if certain conditions are present.
OR
- Option B – You would use equipment able to control the process. These analysers are reliable, accurate and repeatable enough to do that and with the correct installation location and signals connected to the fillers PLC, more than capable of providing accurate information to control the line during start up and running conditions. In this case the installation point of the analyser would be different where it would be located in recirculation on the last buffer tank, this way the analyser can be used when priming the line to control from the very start of the production. This concept is widely known in the industry as pump and run (or prime and run), so the line is primed with beverage and once the analyser gives the OK the product is in specification the line runs. This saves on waiting 10-20 mins for a laboratory assay in order to approve the beverage is OK to run.
How does the product portfolio impact analyser selection?
Establishing the type of product portfolio the bottler is producing is also a very important part of the analyser selection process. Because analysers have varying capabilities it is critical to establish the beverage types that will be running on that specific line to align the analyser performance and capabilities to the product portfolio.
There are many product types but they can usually be broken down into 3 specific categories:
- Regular sugared beverages these are typically in the range of 8-12 Brix (% sugar),
- Low sugared beverages typically in the range 0-8Brix (%sugar), and in this category there are some hybrid sugar plus artificial sweetener.
- Diet or non-sugared beverages that would use an artificial sweetener and these are typically in the range of 0-0.2 Brix (0-2000mBrix)
Analyser choices – Regular, Low sugar and Diet
If you have determined that the production line to be analysed will run all the 3 product types mentioned above, then the obvious choice for your inline analyser is the Maselli IB08. This modular device has the capability to measure the Brix and CO2 content of the beverage portfolio with many optional analyses that can be fitted to the system, such as sugar inversion, dissolved oxygen, PH, Conductivity and more. The analyser can be connected to the plant PLC and also has its own in-built software package (Multilab 8) that will collect and report the historical data from the line in a format required to integrate with any bottling companies data management system. The Multilab 8 software is a very insightful tool providing the bottler process performance calculations allowing them to highlight where potential savings can be made.
Installation point selection with the Maselli IB08
Having determined the IB08 is the correct analyser for your product portfolio you should now determine how the analyser is to be used. As mentioned above beverage analysers can be used as simple monitors or become a far more powerful tool in helping bottlers control their process. Below is an outline of how the IB08 would be used in these scenarios.
- Option A Install in the main process line after the pump which is sending product to the filler. This configuration would allow the bottler to only use the analyser after the main valve to the line is open and the line booster pump is running, therefore the analyser is used as a monitor to allow corrective action to be taken manually or automatically should the product deviate from specification. In this type of installation a typical line start up would mean waiting for an analysis of the beverage in the buffer tank, or filling the first few bottles and waiting for the lab analysis before starting production on the line. This process can take 5-10mins for regular production and up to 20 minutes in the case of Diet Beverage production.
- Option B Install in recirculation on the buffer tank. This installation is prior to the booster pump and prior to the valve allowing product to the filler. In this configuration the IB08 beverage analayser can be used once the line is primed to immediately begin analysing the product. The IB08 analyser has an extremely high accuracy so even when Diet production is in place the control of the concentration of the beverage can be controlled. Using the analyser with this installation allows the bottler to measure the product as soon as the line is beginning to be primed. So as soon as the beverage hits the final buffer tank the analyser will see the product and start to analyse the Brix, Diet or CO2 value. Once the product is within specification the line can run based on the IB08 values. This type of installation allows the bottler to save the time taken for the lab analysis so up to 20 minutes of production time. This type of installation allows for process control, from the very beginning of the run to the very end, giving the bottler not only production time savings but product quality and yield benefits.
Maselli recommends using the second installation method (b) as the bottler benefits by controlling product changeover from the very beginning and also having the capability to measure Diet beverages along with low and regular sugared varieties.
Analyser choices – Regular, Low sugar only
If your production line will only run products with low or regular sugar, then Maselli has an alternate analyser that can be used in these types of production environments, this version of inline analyser is the Maselli IB07. Comprising of a Brix analyser and dissolved CO2 analyser the IB07 is also a modular construction where additional analysis modules such as sugar inversion, dissolved oxygen, PH, Conductivity could be incorporated. The system is designed to be a fully inline installation with no bypass pump required. Like other Maselli products the IB07 can be connected to the Multilab 8 software program so that data from the analyser can be captured and a historical record kept of the line. The software also has the capability to generate reports on the line performance.
Installation point selection with Maselli IB07
As the IB07 is a fully inline beverage analyser it is recommended to install the equipment in the main beverage line after the booster pump which is sending product to the filler. In this configuration the IB07 can monitor the process and provide the necessary feedback and alarm contacts in order for the process operators to be notified of deviations from the specification. Normally the IB07 would not be used for control of the process when in this location. Due to the installation in the main line to the filler the IB07 is also unable to handle monitoring during product changeover but simply a monitor to alarm out of specification beverage. The IB07 therefore is a lower cost solution but obviously the trade off with that is you have less capability for optimizing the process.
Innovative Beverage Analyser Control Panel
The Maselli IB08 and IB07 can be connected to the new MP06 control panel. This touch screen HMI allows the operator to visualize the real time production data. Running a version of the Maselli Mulitlab 8 software the MP06 also has the data to store the data historically and with various I/O options can send the data to the local network or to the cloud. The MP06 control panel can also hold the products run on the line in product recipes, these are stored in the on-board memory and can be selected either on screen or via a remote input. The recipe would hold information like product name alarm limits and historical information for that product.
In addition to these features the MP06 has one additional benefit: an in-built wifi hotspot. This means when remote access is needed to the beverage analyser Maselli engineers can help configure or commission the system remotely, provide training to the local operators and technicians, or conduct system maintenance. This can be done easily without the need of a connection to the plant network. The user simply connects to the MP06 with their mobile phone and remote access can be gained which is a first for such a device in the industry.
The MP06 may be connected to line PLC and / or the M8 software in the laboratory for automatic handling of product recipes. The operator can send a recipe from the PLC when starting a new run, or this can also be programmed to happen automatically from the filler PLC. Alternatively the recipe could be sent from the Laboratory version on Multilab 8 software. A very versatile system.
A Final Word
In the rapidly evolving beverage industry, precision and efficiency in production are key. Maselli offers two state-of-the-art solutions – the IB08 and IB07 beverage analyzers – each designed to meet different needs within the industry. Whether your goal is to simply monitor product specifications or to have a comprehensive control over your beverage production process, Maselli’s IB08 and IB07 provide robust solutions. By understanding your production needs and the capabilities of these analyzers, you can make an informed decision that enhances your production efficiency and product quality. Contact us if you would like more information or would like discuss the subject in this blog.
Equipment referred to in this article
-
Beverages
IB08 – BEVERAGE ANALYSIS SYSTEM
-
Beverages
IB07 – Beverage Analyzer