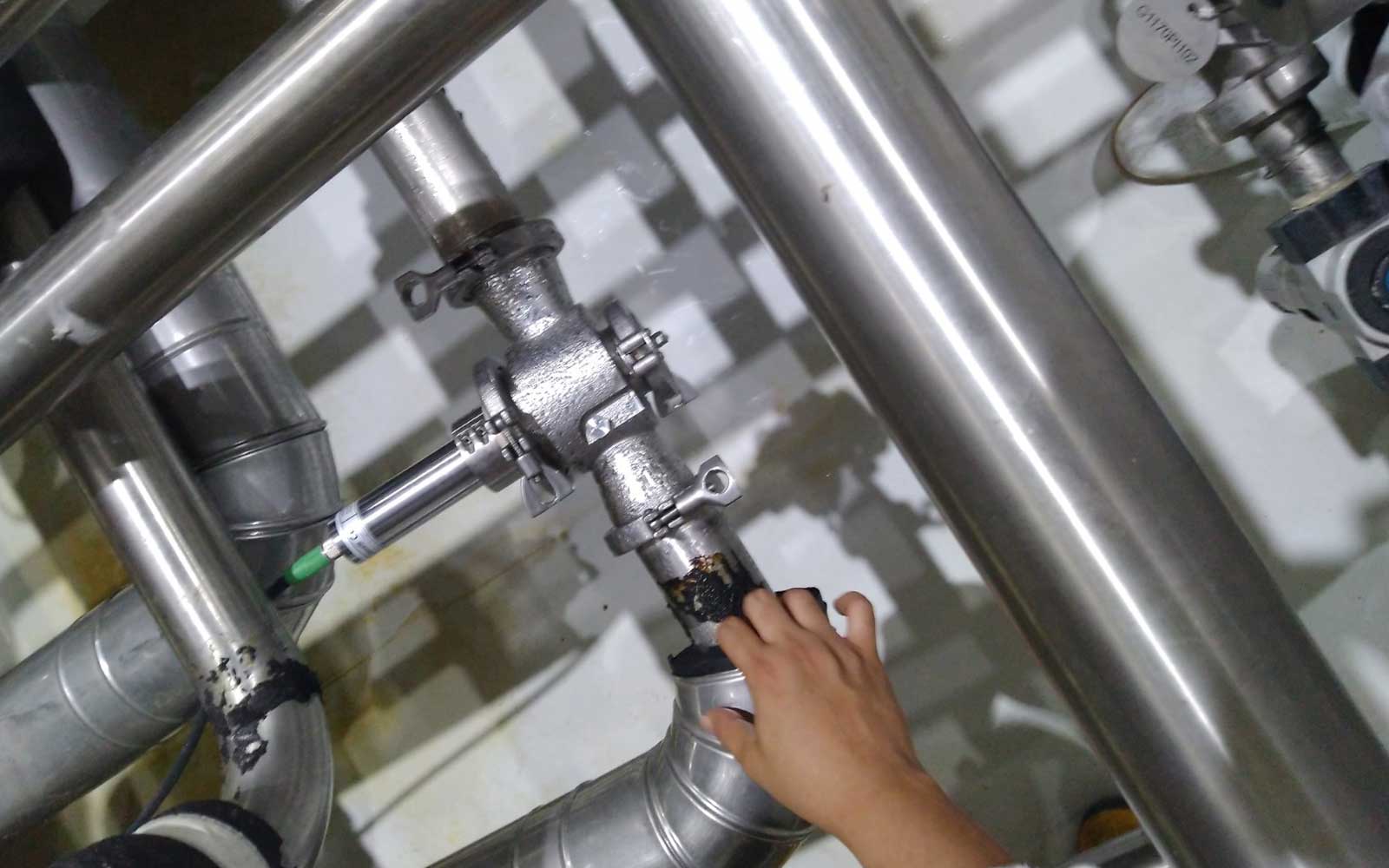
Glycol concentration analysis
We were recently asked by a pharmaceutical client to test if it would be possible to use a Maselli UR62 process refractometer to monitor the concentration of the glycol in the refrigeration system.
Application information
Factory type: Pharmaceutical plant.
Process: Refrigeration system: ammonia based refrigeration system
Installation point: Glycol mixing tank
Installation
The UR62 unit is installed in the return pipe to the buffer/dilution tank, before the fluid is sent to the cryogenic system (coolant liquid). Important note: this is an example of a complex refrigeration system, with the possibility to divert the coolant liquid in different areas, opening and closing valves
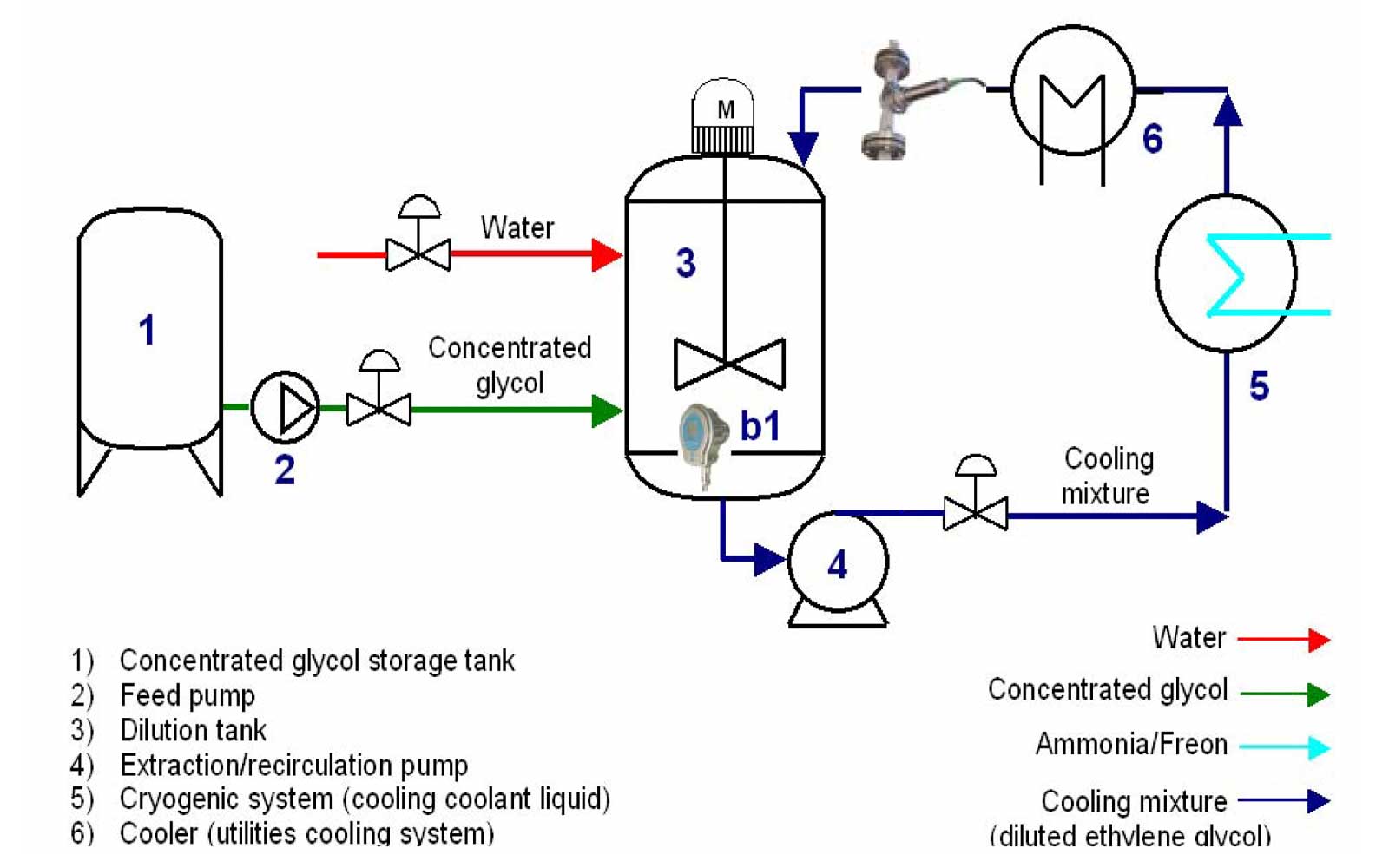
Results
The graph shows ten days of production (including one weekend). In this period the concentration of the glycol in the circuit has been regenerated two times (see the blue line in the graph), due to its continuous dilution. The dilution is due to the fact that the glycol is strongly hygroscopic so that, when it is in contact with air, it captures the water vapour. Therefore the UR62 process refractometer can detect this and allow the concentration strength to be kept consistent automatically.
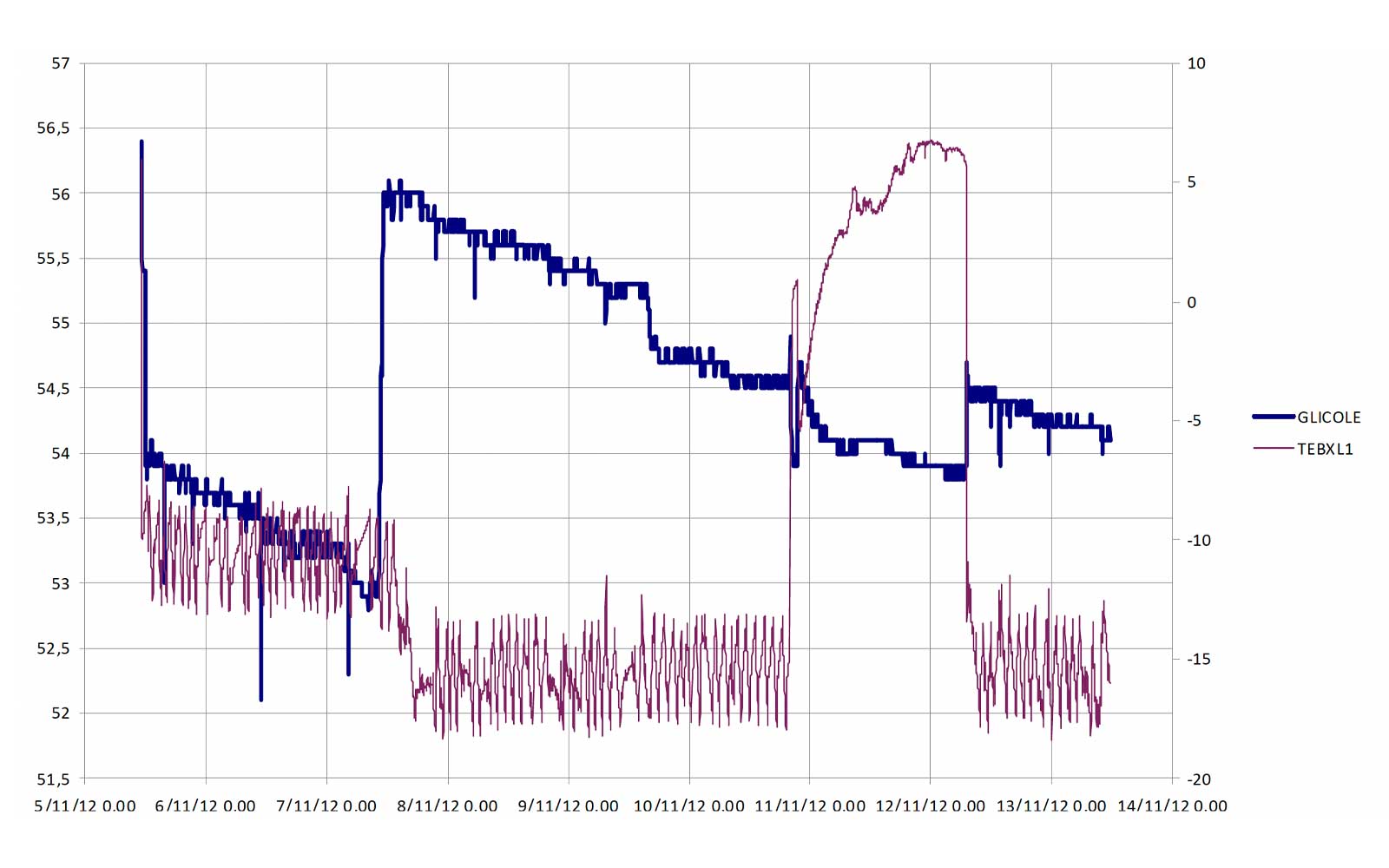
Return on Investment
In an average plant, in normal conditions the pay-back of the unit can be calculated in 6 to 12 months.
Conclusions
The test proved that the concentration of the glycol inside the system slowly but continuously decreases. Therefore an in-line analyser continuously monitoring and controlling the glycol concentration is extremely useful and has payback benefits with a fast ROI.
Applications across other industries
All plants having an industrial refrigeration system (in the food/beverage, pharma and chemical field) can benefit from this technology. We would be happy to discuss the potential benefits with you if you have a refrigerant system described above.
The UR62 process refractometer can be applied to the plant by the OEM of the cooling systems before delivery, or retrofitted to the plant after installation. JWII staff would be more than happy to assist you if you have this type of application in your facility, please feel free to contact us for an obligation free discussion.